New depot, new culture
A tour of National Express West Midland’s Perry Barr depot
Making the move to a new depot is potentially a massive upheaval for an operator. This is especially the case with a well-established site and National Express’ old Perry Barr facility certainly was that, having been continually operated from for just over 90 years. The fresh depot is the first National Express bus depot to be built since its Coventry facility was constructed in 1986. The focus on the new site is to reduce the operation’s carbon footprint and to put in place a state-of-the-art, future-proof facility.
During a tour of the new site in north Birmingham, Karen Jackson, National Express West Midlands Head of Transformation, said the relocation involved not just a change of site, but a culture change too.
Staff were included in the project, even given a say on colour schemes. Work started on the site in July and September 2021 for enabling works and full construction works respectively.
One of the goals of the move to the new purpose-built site was to improve working practices, a big part of which was to make sure staff were all onboard with that. Karen said: “We made sure we brought over all of the processes that worked in the old site and did a leadership workshop and we put in place daily stand-up meetings as part of our new discipline.”
All drivers were given a tour of the site before moving, including the chance to drive a bus in and out of the depot to get used to it. “You have to make sure people feel confident,” said Karen. “We had to get all staff to register their number plate for the car park barrier. Getting everyone to do that on day one was like herding cats.”
There was no extra support in terms of additional staff during the relocation, running services as it made the move. Services started from
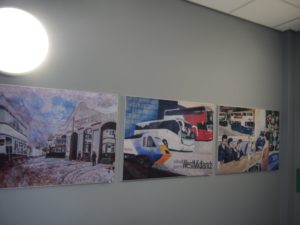
Artwork on the old depot’s walls have been reproduced and displayed in the new site
the site on 11 December 2022. Making the situation even more challenging was the snow on the second weekend of December. Despite this, the team pulled through and got the job done.
Staff wellbeing was key when the site was designed, according to Karen. In the driver muster area, she said security is taken very seriously, with key fobs for drivers. It has a light and airy atmosphere and has been designed as a communal space for employees. It is open plan, avoiding a ‘them and us’ feeling between drivers and office staff. The better visibility it affords also means drivers’ wellbeing can be better monitored as they log in and out. Digital information screens in this part of the building replace the paper noticeboards from the old depot. If staff have any issues or questions, they can make their managers aware using the Slido app.
Nearby the muster area is the support office, where daily stand-ups take place to brief staff. The operations and engineering managers have been brought together in this space, having been located separately in the old site, leading to more collaborative working.
Heading upstairs on the way to the staff canteen, there is a series of painted murals recreated from the originals on the walls of the old depot. Also surviving from the previous site were two snooker tables in the canteen. Karen said: “We worked with BAM [the principle contractor] to make sure it didn’t feel like a school canteen.”
National Express has teamed up with a local cafe for its food offering, which includes breakfast, lunch and dinner. As well as the food on offer, there is also a quiet room aside from it for prayer or a bit of peace and quiet.
The canteen area serves as a community area for staff too.
Staff are also taken care of in the training area. There are several classrooms where National Express West Midlands puts its staff through Driver CPC and other courses.
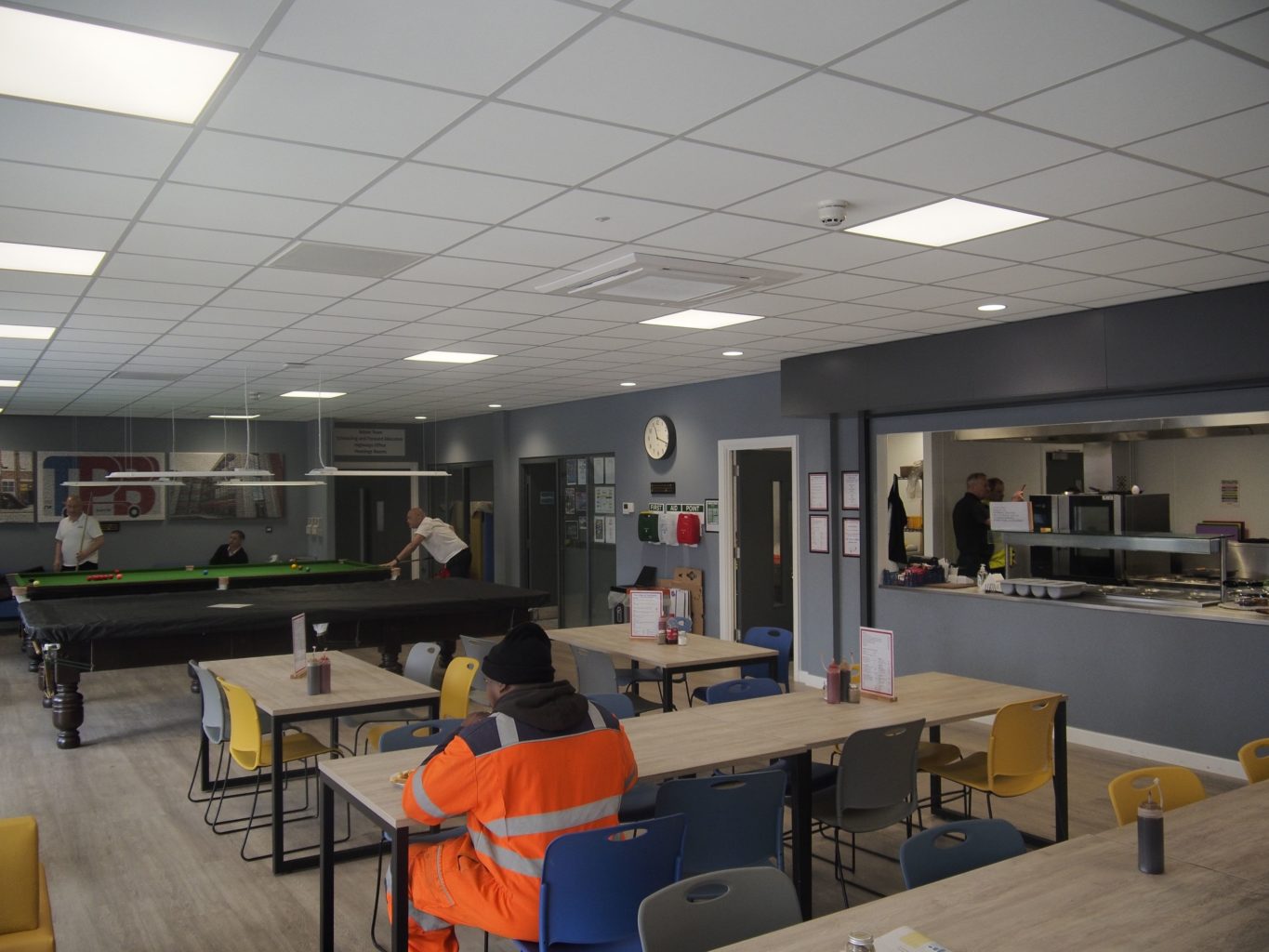
The canteen has been designed to be as much a communal area as it has a place to eat
Driving simulator
One of the training rooms houses the operator’s driving simulator, thought to be the first of its kind in the UK. The DriVR system from Spanish company Simfor consists of a driver’s seat kitted out with a steering wheel, accelerator and other controls, replicating the cockpit of the operator’s Volvo buses. Screens surround the set-up, replicating the windows of a bus, including the view from the mirrors. Similar to a computer game, trainees guide a bus around digitally rendered roads, interacting with the equipment just as they would a real vehicle (turning the wheel, depressing the accelerator, hitting the brakes, etc). The trainers can add obstacles, change the weather and affect traffic levels. The simulator is programmed to replicate the drive and performance of the buses in the operator’s fleet as closely as possible, even altering them when adverse conditions are in play, such as snow and rain. For added realism, the seat has haptic qualities, simulating the movement of the bus as it drives. A headset creates an even more immersive experience, providing full virtual reality, not just in the driver’s seat but even walking around the virtual bus.
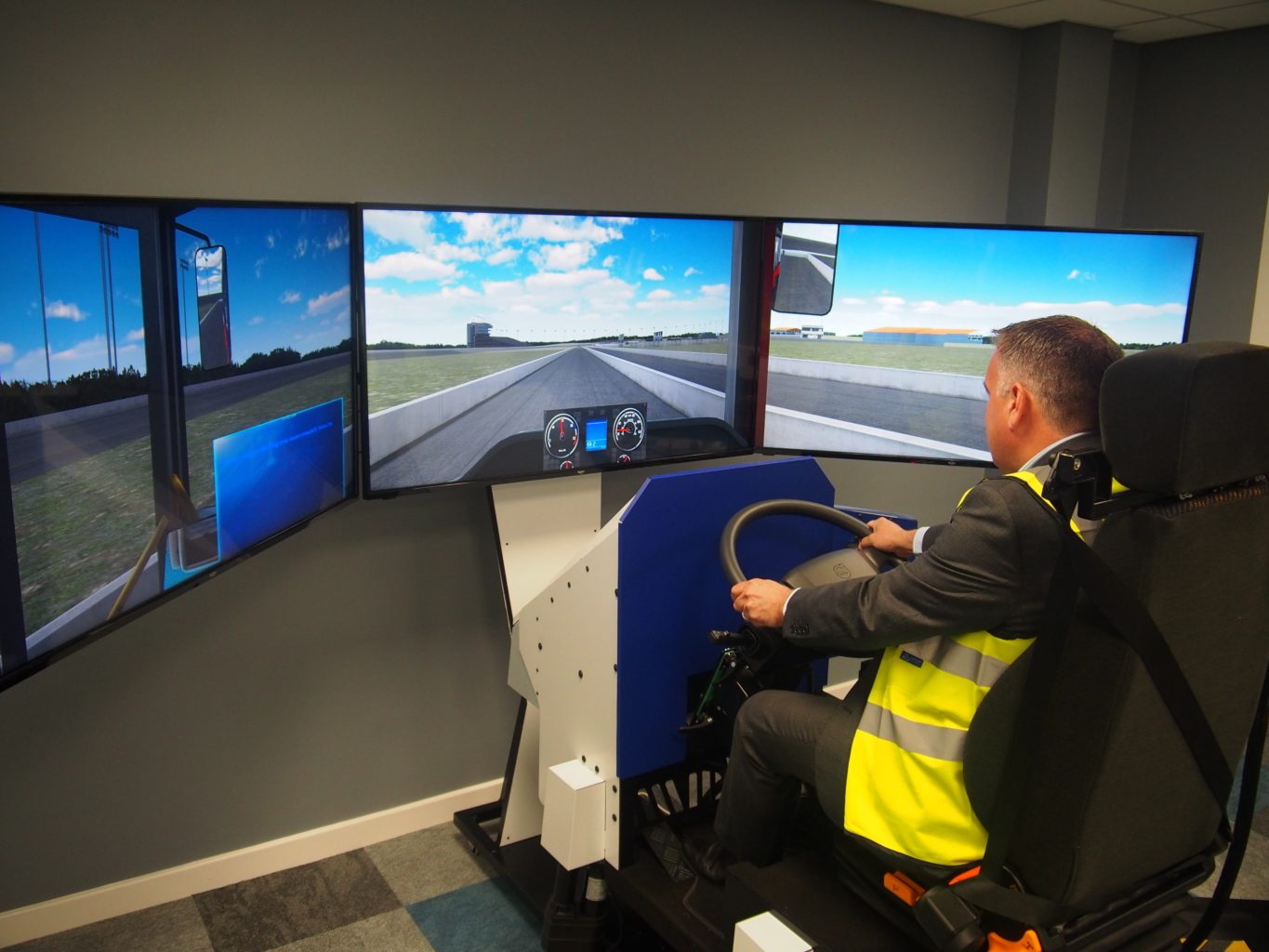
The bus driving simulator on the site provides a risk-free place to train potential drivers
Jenny Tocknell of the DriVR simulator team said the company has already had a number of success stories as a result of it. The system was at a job shop event recently and it attracted 12 people to sign up to the company’s driver training process on the back of trying out the simulator.
Jenny said: “I think the real misconception is that it can be very daunting to drive a bus. But when you get into the virtual cab, you soon develop the skills. It’s just about breaking down those barriers.”
Feedback about it from people who have tried it has been very positive, according to Jenny. She said: “It’s risk-free training. We did a Google review and 100% recommended it to their colleagues.”
National Express’ Coventry depot also has one and since its installation, there has been a 20% reduction in collisions, according to Jenny.
Engineering
Significant investment was made in the engineering side, in particular in new equipment. Before entering the engineering side, there is a side room, used by the mechanical team for meetings. This is part of the culture change in the depot, with stand-ups being carried out by the team in this part of the operation too. Deputy Engineering Director, Nick Sorrill, said: “Here we can take feedback or talk about any problems. It’s a nice area to have.”
There are three separate workshops in the depot, one of which has double-length Premier Pits maintenance pits installed, making them capable of taking articulated buses if needed. This workshop bay also has a DVSA approved ATF lane installed, meaning it can carry out MOTs. There is a potential possibility to hire this out to third parties.
Being able to build a new site has enabled National Express to build a safer, more efficient layout that was not possible with a site over 90 years old.
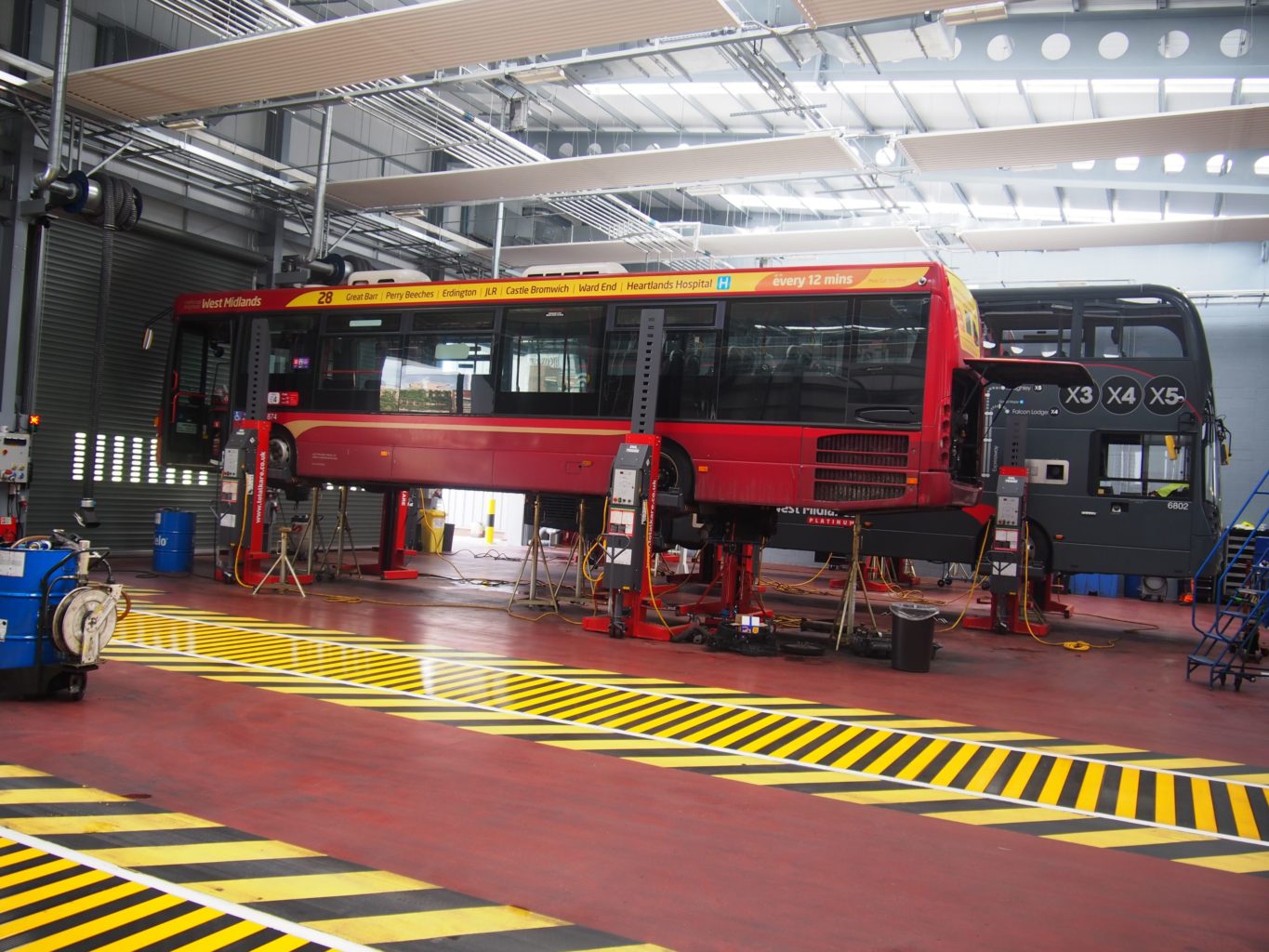
A combination of Premier Pits prefabricated steel pits and Totalkare vehicle lifts are used for maintenance and repair
All new workshop equipment has been purchased in this area. Lube reels have been installed and a tug has been purchased to pull non-starters into place. As well as pits, the engineers also make use of Totalkare vehicle lifts, used in combination with axle stands. The company has opted for plug-in lifts as opposed to wireless versions, with technicians at the site preferring not to have to charge them.
Nick said the business takes care of all work that would take up to eight hours, such as running repairs, internal repairs and planned maintenance. But if it is a major unit change, they will go elsewhere.
Outside of the workshops and in the yard, there is the capability to install enough provision for up to 170 electric buses, with spaces ready for chargers to be dropped in. The company already operates AD/BYD electric buses, with the infrastructure managed by Zenobe.
Nick praised the fact the yard has been given good lighting and a more efficient parking plan than the last site. Also, a separate washing and fuelling lane means the team can do their work away from operations.
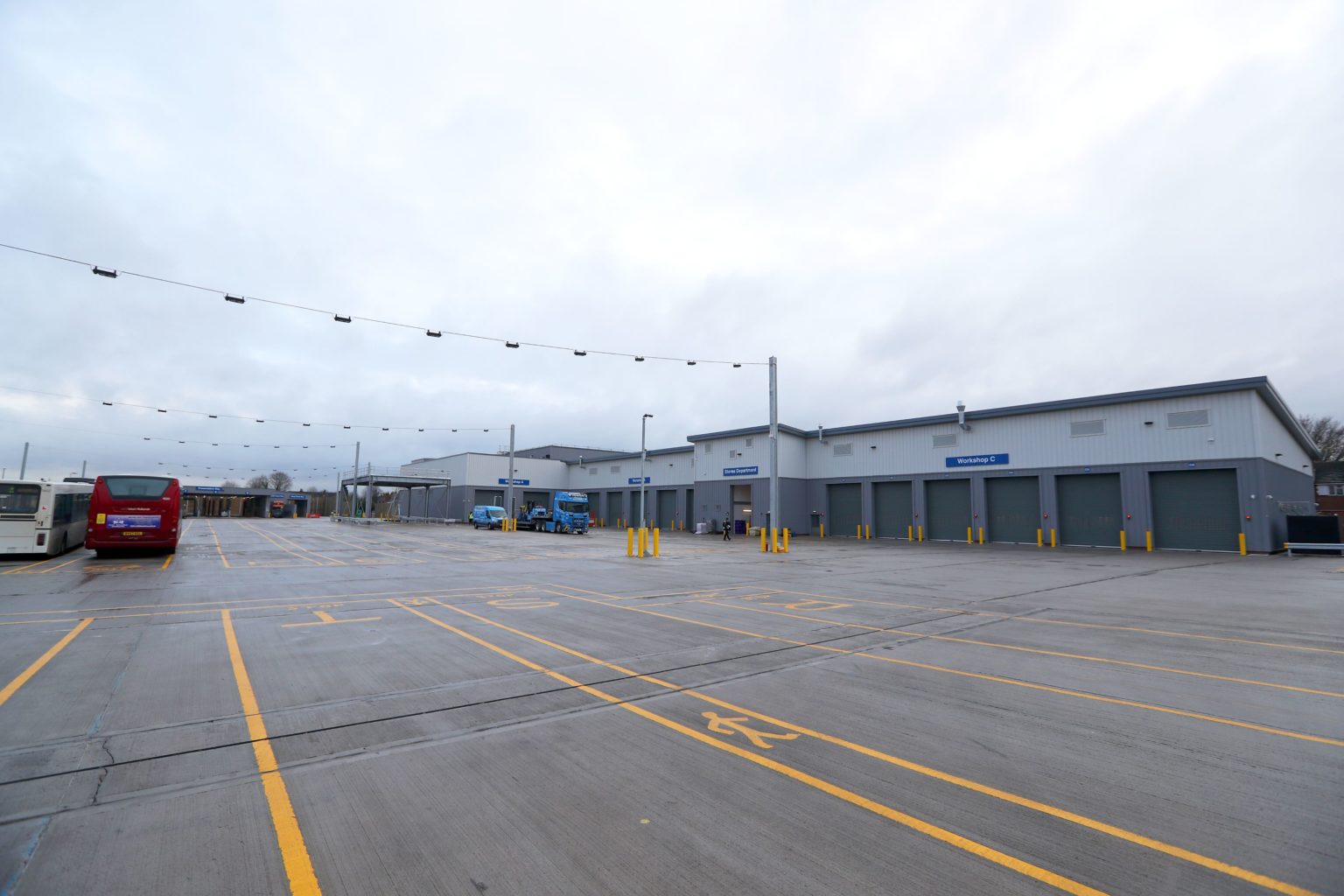
There is room to park for the 150 buses running from the depot
The ground of the site is heavily contaminated owing to its industrial past. Construction company, BAM, went to great measures to avoid any negative affects of this contamination, denying any potential harm using a bed of concrete.
Acoustic fencing has been put in place in consideration of the nearby residences. Colin Harper, Project Manager, BAM, said: “Noise from the depot was actually found to be quieter than the noise from everything else in the area. We made sure the impact on the local environment is minimal.”
National Express Perry Barr in numbers
- Employees – over 450
- Buses running from the site – 150
- Routes served – 20
- Bus parking spaces – 171
- Electric vehicle bays – 14
- Solar panels – 150